At House Of Horvath in Toronto, Canada, the manufacturing of cigars has taken place continuously since the year 1977. Since that time, they’ve employed a very unique mechanically-assisted old world process to craft their cigars on machines that have been out of production for over a half century.
The following piece will take a look at the highly intricate mechanized process of making Bandi Corona Claro cigars at House Of Horvath, and a small duo of crackpot mechanics that work tirelessly to fabricate components by hand to ensure that the antique cigar machines run smoothly.
All In The Family
Having recently celebrated his 70th birthday, HOH Head Mechanic Dominic Bono has been a fixture at House Of Horvath since 1987.
As a long-standing employee, Bono follows in the footsteps of his mother Antonia, who was first hired back in the late 1950s under the Joe Horvath Sr. for his Ontario Tobacco Company, which was ultimately sold to the MacDonald Tobacco Company years before the establishment of House Of Horvath in 1977.
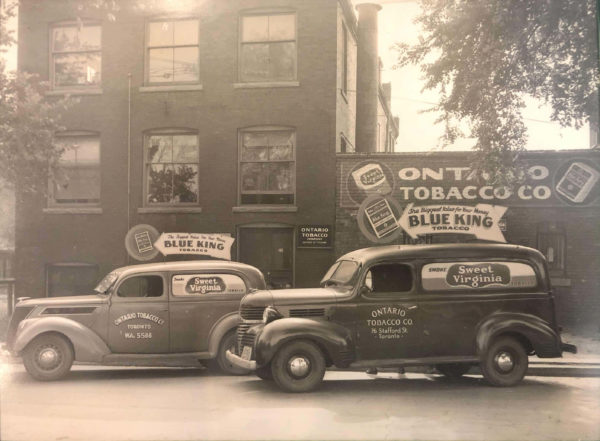
The Ontario Tobacco Co. was established by Joe Horvath Sr.
In all, Antonia devoted 25 years of service for the Horvath family, and left her son to continue on long after she left.
Having passed away in 2014, little did she know that he would remain there for over 35 years and counting.
Mechanically Inclined
When he first began, Bono was trained entirely by House Of Horvath co-founder, Leslie Albert Sr., a crafty mechanical engineer who married Joe Horvath Sr.’s daughter and left his work at a Toronto plastic moulding company to work full time in the tobacco business.
“After I was hired, I was trained by Albert Sr. In total, it took a good three to four years for me to be able to comfortably handle things on my own” says Bono. Though Bono had no prior formal training, he had 2 brothers who were educated as auto body mechanics and had worked in garages.
At the time, the House Of Horvath factory had roughly 15 workers, and ran 6 cigar rolling machines as well as additional stripping and packing machines to make an assortment of cigars that were produced typically in panetela, corona and super corona sizes. In addition to this, they were also making private label cigars for numerous outside enterprises.
Several decades before in the 1970’s, 4 of the machines had been purchased by Joe Horvath Jr. and Albert Sr. from the closure of Simon & Sons cigar factory in Montreal, Quebec.
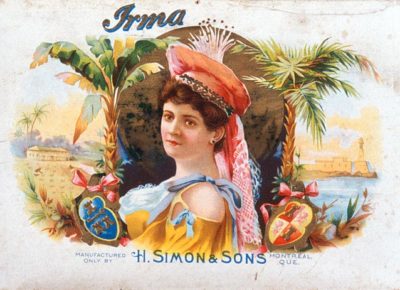
A vintage box liner for the Simon & Sons’ ‘Irma’ cigar
The remaining 2 machines were purchased from Stanford Newman of the J.C. Newman Cigar Co. in Tampa, Florida.
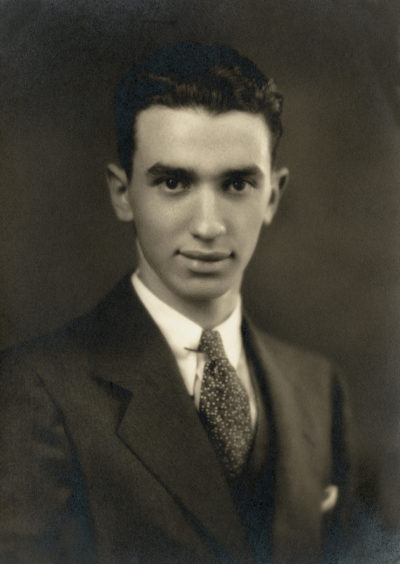
Second generation cigar maker Stanford Newman
Since then, they have continued to serve as the sole type of rolling machine used for making cigars at House Of Horvath.
The six machines, which are now over a century old, were initially made by American Machine & Foundry. AMF was also recognized for manufacturing a wildly diverse array of mechanisms that ranged from bicycles to yachts to atomic reactors.
They even once owned Harley Davidson.
“AMF was also recognized for manufacturing a wildly diverse array of mechanisms that ranged from bicycles to yachts to atomic reactors. They once owned Harley Davidson”.
A New Wingman
These days, Domenic Bono has a fellow mechanic wingman: North Korean-born Sung Lee (known as strictly ‘Lee’ by employees).
Lee started in August of 2020 and has never looked back, stating that he is “very happy” with his work at HOH.
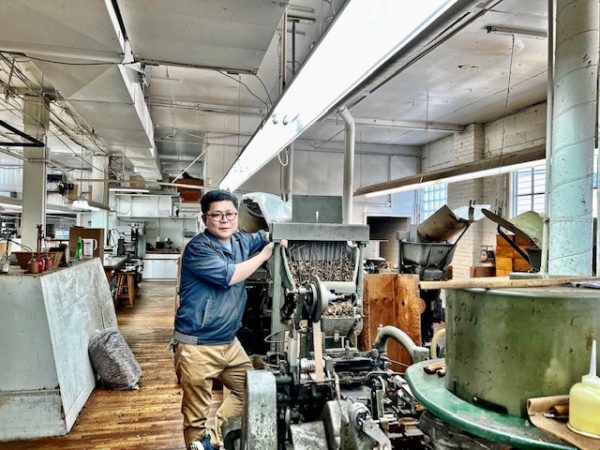
HOH Mechanic Tsung Lee
In 2006, Lee fled Communist-run North Korea for a better life in South Korea, and alongside other defectors actually traversed a frozen lake in the middle of the night while being “shot at” by North Korean soldiers.
“We left in the middle of the night to walk across frozen water in wintertime in January. We could hear the loud popping sound of gunfire behind us. Thankfully we were not hit – we made it!”.
After obtaining numerous licenses for building and mechanics in South Korea, Lee left for Canada. Lee found soon work making electrical control boxes in Mississauga, Ontario while spending time reacquiring the very same licenses on Canada soil, as sadly the Korean-issued ones were not recognized in Canada.
Today Lee works alongside Bono to routinely fabricate individual parts out of metal for the machines after they break down. As the machines are over a century old and are no longer in production, the replacement parts required are also no longer in production either.
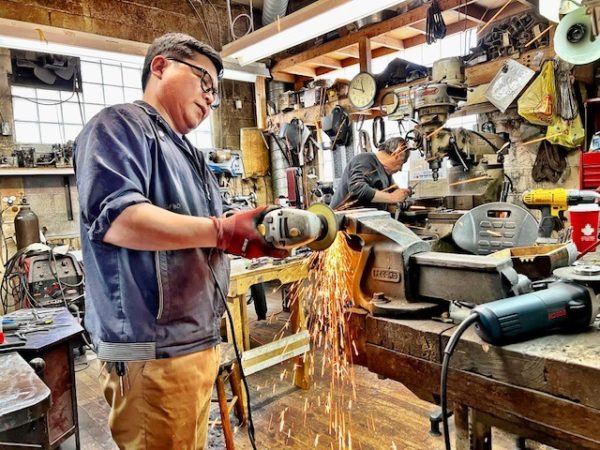
Sparks fly: Lee and Bono in their workshop
Bono says that in less than 2 years Lee knows more than any of the 5 previous apprentices he has had working under him throughout the past.
“You teach Lee something and he absorbs it fast. We had people who had been here for 5 years and they knew barely half of what Lee knows now. Of course they all left because they just couldn’t hack it” states Bono.
A Well Oiled Machine: Collaborating With The J.C. Newman Cigar Company
“We aim for making around Bandi 9,000 cigars a day” says HOH Productions Manager Joseph ‘Zac’ Costa, who goes on to inform that the overworked machines run 7 hours a day for 5 days a week and are prone to frequent breakdown. “When the parts break down, they typically have to be manufactured right here on site. Arms and cams regularly break down and must be welded back together because we just can’t get them anywhere” says Costa.
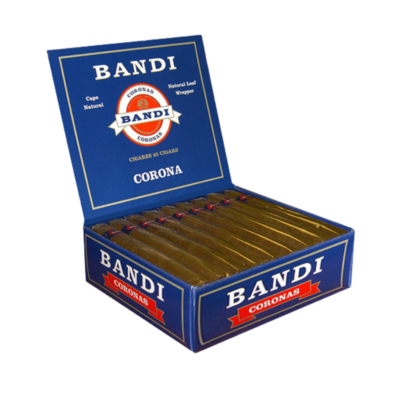
A box of Bandi cigars
Prior to 2019, the HOH rolling machines would routinely break down and require rebuilding every 1-2 months.
Thankfully, through correspondence and a careful comparison of notes with the mechanics at the J.C. Newman ‘El Reloj’ Cigar Factory (who also still use the very same antique machines) in Ybor City, Tampa, Bono and Costa were able to greatly improve upon the rolling processes at House Of Horvath to cut the frequency of breakdowns to roughly once a year.
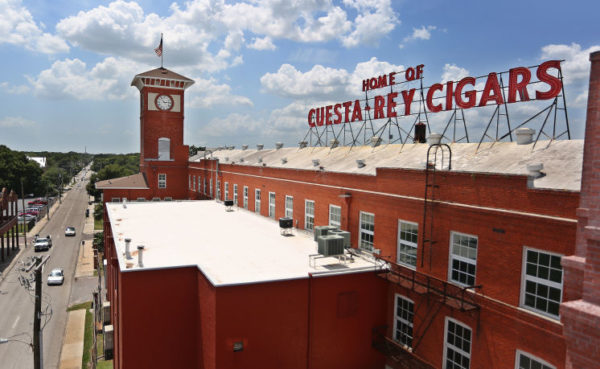
The El Reloj Cigar Factory in Tampa, FLA
Bono and Costa found out that by adding very frequent applications of simple mineral oil throughout each day, the factory was able to increase their production and decrease the occurrence of breakdowns with their rolling machines. The mineral oil doesn’t affect the taste of the tobacco and is now applied 5-6 times each day.
“To make sure that the rollers are regularly applying the oil, we have a bell that sounds throughout the day as a reminder. Oiling those machines regularly is of huge importance” says Costa, “We got that from the Newmans”.
At 6:30 AM, Lee is the first one in the factory and delivers the first applications of lubricant. For the remainder of the day, the all-female rolling staff must apply the remaining applications.
Machine breakdowns weren’t the only thing the J.C. Newman Company has provided a helping hand with.
In 2020 the cigars were suffering from what Costa can only describe as a “candy cane effect”, whereby the wrapper becomes spaced out and exposes a ‘swirl’ of rough binder underneath.
After a trying numerous adjustments and even forging new parts, the problem continued to persist for upwards of 6 months until collaboration with the Newmans proved to identify and correct the problem.
“We left in the middle of the night to walk across frozen water in wintertime in January. We could hear the loud popping sound of gunfire behind us. Thankfully we were not hit – we made it!”
The Future Of An Old World Process
In July, the House Of Horvath factory will implement their annual forced factory shutdown for the duration of a full month to rest the machines.
“It’s kind of like Santa’s Workshop in January” states HOH Vice President Colm O’Shea with a chuckle. “It allows us to rest our cigar makers and rest our poor machines so that we’re ready for the year ahead”.
For Bono and Lee however, there’s no rest for the wicked.
During shutdown the two will diligently perform a complete top-to-bottom disassemble and rebuild of each machine to ensure that they are in top shape for the 11 busy months that will follow.
When asked about retirement, Bono says that he’s unsure when he will hang up the welders mask, but is confident in Lee’s ability to ultimately take over the helm.
“He may need a second set of hands from time to time, like when a cam breaks, you need more than one person. Other than that, Lee is so good that he could probably handle it all on his own” says Bono smiling.
Of course, like all things – only time will tell.
Wonderful article! Love your cigars! K